Some research has shown that only 15% of employee errors are caused by the employees themselves. The remaining 85% of errors are caused by factors beyond their control.
Unfortunately, some managers tend to blame employees without addressing the real causes of the problems. This approach, besides not solving the problem, can create a culture of fear in the workplace. Employees become discouraged from being proactive and tend to hide any mistakes they encounter. Therefore, it is crucial for managers to recognize and address these systemic causes of errors to create a fair working environment where individuals are not disproportionately blamed for mistakes.
Employee errors can have a significant impact on business, leading to inefficiency, reduced productivity, and potential financial losses. To effectively solve this problem, it is key to understand the underlying causes of these errors. By identifying and eliminating these causes, managers can create a work environment that minimizes errors and promotes success. In this blog post, we will explore six common causes of employee errors and discuss strategies to eliminate them with the help of tools provided by Workanizers.com.
1. Unclear Procedures
Clear and well-documented procedures are key to guiding employees in their tasks. When procedures are unclear, incomplete, or difficult to access, errors become inevitable. Employees may struggle to understand the correct steps to follow, leading to mistakes. To solve these problems, managers need to establish procedures that are understandable and easily accessible to employees. This can be achieved with the help of management tools [Workanizers.com], which assist in properly documenting processes and procedures and ensuring easy access for employees.
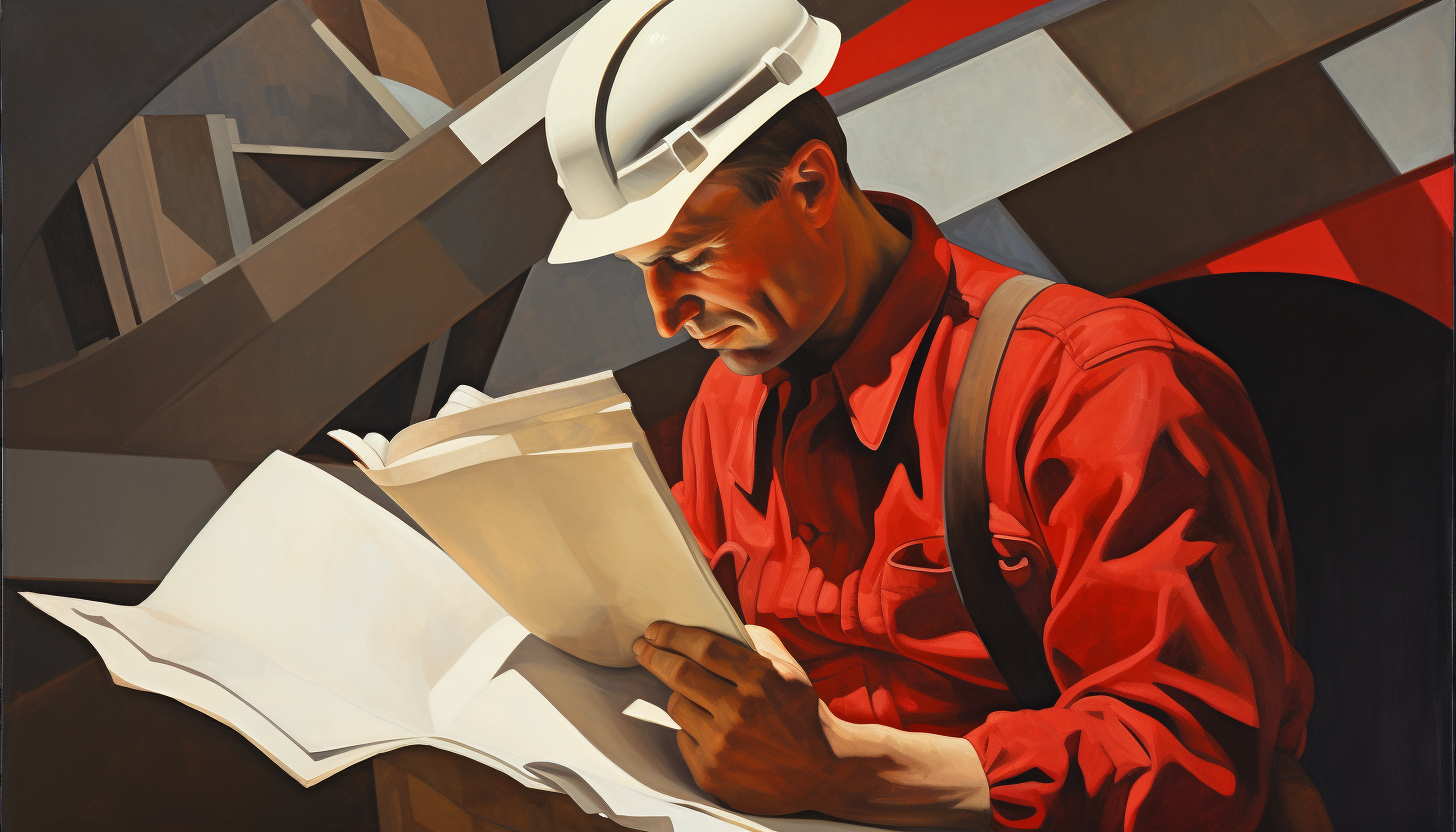
2. Inadequate and Complicated Processes
Processes present us with established and tested paths to achieve goals. They represent sequences of connected tasks that lead to the products and services we deliver and charge for.
The truth is that employees are usually only engaged at the task level. However, the process as a whole provides the results we have set. For a smooth flow of work, it is necessary for tasks to be simple and logically connected, without loops, and without many variations and sub-variations. But most importantly, they must be interconnected by clearly defined handover points for results between two tasks. Particularly in cases where 2 tasks that follow each other are performed by 2 different employees, misunderstandings and mistakes arise, leading to time lost and creating antagonisms among employees.
Processes in a company, over time, become inadequate. There are several reasons for this.
- Business circumstances change slightly, but processes have not changed. Then it is up to the employee to improvise, and mistakes occur.
- Processes are continuously upgraded to avoid mistakes that occur within them. Still, it would be more appropriate to eliminate such mistakes through adequate employee training rather than changes in the process.
- In the process, there are too many tasks where a choice has to be made between, for example, 2 directions in which the process continues. These are the points where the sequence of the process should be interrupted, but this does not happen.
- There is an attempt to use one process for multiple similar jobs. This is usually due to the inertia and sluggishness of managers. Thus, variations for different similar jobs arise, and the entire process becomes unclear because it should be represented with several different processes that provide precise directions for performing a variant of the job.
- Processes are changed on the fly without being documented, so it is not known which version of the process is current and correct to follow.
- Employees are not adequately informed about the current processes, i.e., which are valid.
- Documented processes do not exist, so orders are given on the spot to the employee about which tasks to perform in sequence. This can yield results for a while, but when orders are absent, the employee stops and waits or takes the initiative to proceed through the process. Again, misunderstandings and mistakes arise. More experienced employees can manage, but this requires years. In today’s business, such a luxury does not exist when hiring new labor.
- There are managers who pride themselves on complicated processes and thus give themselves importance. And they avoid simple processes because they feel superfluous in them. The reality is the opposite. The greatest skill and most knowledge are required to build simple processes, and they can be automated and performed with a minimum of errors.
3. Inappropriate Employee Profile
When hiring, each employee has certain characteristics that we need for them to perform certain jobs, i.e., execute tasks. These characteristics are subject to change over time. We pay attention to their knowledge, experience/skills, and personal traits.
It is impossible to expect that every employee can perform all tasks. Even a small mismatch between what the employee should do and what we can expect from their profile increases the likelihood of making a mistake.
There is no company that has optimal profiles for each task. They should be as optimal as possible, and most importantly, the manager needs to know how much they can expect from the employee and be ready to prevent potential mistakes proactively.
Indiscipline and Negligence
When an employee has inappropriate personal traits, mistakes often occur as a result of their negligence. This includes not adhering to rules and methods of work, i.e., operational procedures.
4. Inadequate Training
Training employees to perform tasks properly requires some time and effort. When people do not understand what they are doing or how to do it, there is a greater chance of making mistakes or failing to complete tasks fully. We can reduce this risk by providing our employees with adequate training on how to perform specific tasks with the necessary results.
We should focus on simple and quick training that yields results within just a few days. This can be achieved with so-called “info” training. This is training that presents employees with the procedures for the tasks we expect them to perform. Then, independently or with the help of a more experienced employee, they learn to “read” and use procedures. Any uncertainties around procedures should be clarified during training and later during the first task executions. Such “info” training should be divided into portions for individual or small groups of tasks so that employees can more easily consume them and immediately start using them.
It is important that after training, we achieve a so-called “Agreement on Completed Task” with the employee, meaning that we confirm that we have agreed on the interpretation of what result is expected from the employee.
5. Lack of an Incentive Program
The reward system is there to ensure good results in the future, not just as a reward for what has already been done in the past.
An incentive program must be simple, easy to remember, and verifiable. Only then can be a motivation for the employee during work.
If they have to sit down and retroactively “calculate” whether they deserve some incentives after completing a task, then the incentive program loses its purpose.

6. Inadequate Operational Management
The role of a manager in operational management is crucial for minimizing employee errors. Unfortunately, employees are often largely left to themselves without sufficient coordination and support.
An appropriate manager needs to plan and prepare each task. They must delegate the task to the employee at the right time and provide them with the necessary information, then control the execution, timeliness, and quality of its execution and always be available for support.
Only good managers with appropriate knowledge and experience can synchronously manage the execution of dozens of tasks by dozens of employees and ensure that the entire workflow proceeds smoothly, without mistakes and friction.
Conclusion
By eliminating the causes, we will also eliminate the possibility of employees making mistakes. This sounds logical, but achieving a level of business where employee errors are eliminated is not easy. It requires a comprehensive approach to organization and management.
Using management tools like “Workanizers” can significantly help in this. Proper application of the methodology of organization and management in arranging all aspects of business is necessary to eliminate errors. The comprehensiveness is important because the direct and indirect interconnection of business events in a company is very complex and cannot be intuitively and sporadically followed and controlled without appropriate management tools.
On the other hand, it is important that such a comprehensive approach is not cumbersome, bureaucratic, and slow but rather fast, easy, and simple, i.e., very operational. Only in this way can we achieve professional standards in organization and management that provide practical results.